Soda Fountain Maintenance
Evolution Maintenance
When to repair or replace?
Soda fountain maintenance can be tricky. There’s a lot that can go wrong with soda machines, but there are also plenty of opportunities to troubleshoot your machine before calling in a professional soda fountain repair technician.
Here are a few ways to determine whether you can fix your soda fountain dispenser on your own or if you need to call for backup.
WHAT CAN GO WRONG WITH A SODA MACHINE?
For a process as simple as mixing carbon dioxide, water, and flavored syrup (assuming you have a post-mix machine) and dispensing it into a cup, there’s plenty of room for error and malfunction. Fortunately there are a few things you can try before calling in the professionals?
ISSUE #1: FLAT SODA
What’s soda without fizz? If your soda is coming out flat, there are a couple of possible culprits: temperature and CO2. After powering the soda dispenser down, start with your carbonator. Make sure that it is securely plugged in and operational.
If your carbonator is working, then move on to your CO2 tank and make sure that it still has gas in it and that there are no leaks in the line. If you hear hissing, call for service. Not only are CO2 leaks costly, but in extreme situations, they can lead to suffocation.
Finally, you should check your ice tank: well-chilled water and syrup keeps the carbonation inside the beverage, rather than allowing it to escape into the atmosphere.
If, after turning the machine back on and allowing some time for cooling, your soda is still flat, call a professional repair technician.
ISSUE #2: PUMP WON’T STOP PUMPING
First, figure out which pump is the problem by following the supply line to the source. If you’re running a post-mix (BIB or bag-in-box) system, you may need to replace your existing bag-in-box with a new one, using sanitary best practices as detailed below.
After removing the empty or malfunctioning bag, use a clean food service towel or gloved hands to push the nipple valve on the end of the bag connector into the flavor bag until the pumping stops. Submerge the connector into your drinkable water source until the system re-pressurizes and the pumping stops. Pressing the nipple valve in can help with this process. At this point, you may also try disconnecting the carbon dioxide line as previously explained. If this still doesn’t work, it’s time to call a professional.
ISSUE #3: ONLY SYRUP, NO FIZZY WATER
Make sure the water source is on and that water is flowing to the unit. If water is not entering the unit, look for kinks in the hose that may be restricting water flow to the machine. If not, call a pro.
ISSUE #4: YOUR SODA IS DISCOLORED OR DIRTY
The first thing you’ll want to do is check to make sure that your product has not passed its expiration date. If the product is still “good,” simply run the soda through the unit until the color returns to normal. If, after a few cups, your soda is off-color, you should contact a professional.
If your soda has floaties or dark particles, remove the dispensing nozzle and, using sanitary brushes, clean and sanitize the nozzle and valve with an approved sanitizer solution.
WE CAN HELP WITH YOUR SODA FOUNTAIN MAINTENANCE
If you need to have your soda machine examined by experienced professionals to determine whether or not repair is your best option, the specialists at Evolution Maintenance can help.
Contact us
today at (615)-649-0622.
EVOLUTION MAINTENANCE COMMERCIAL HVAC BLOG
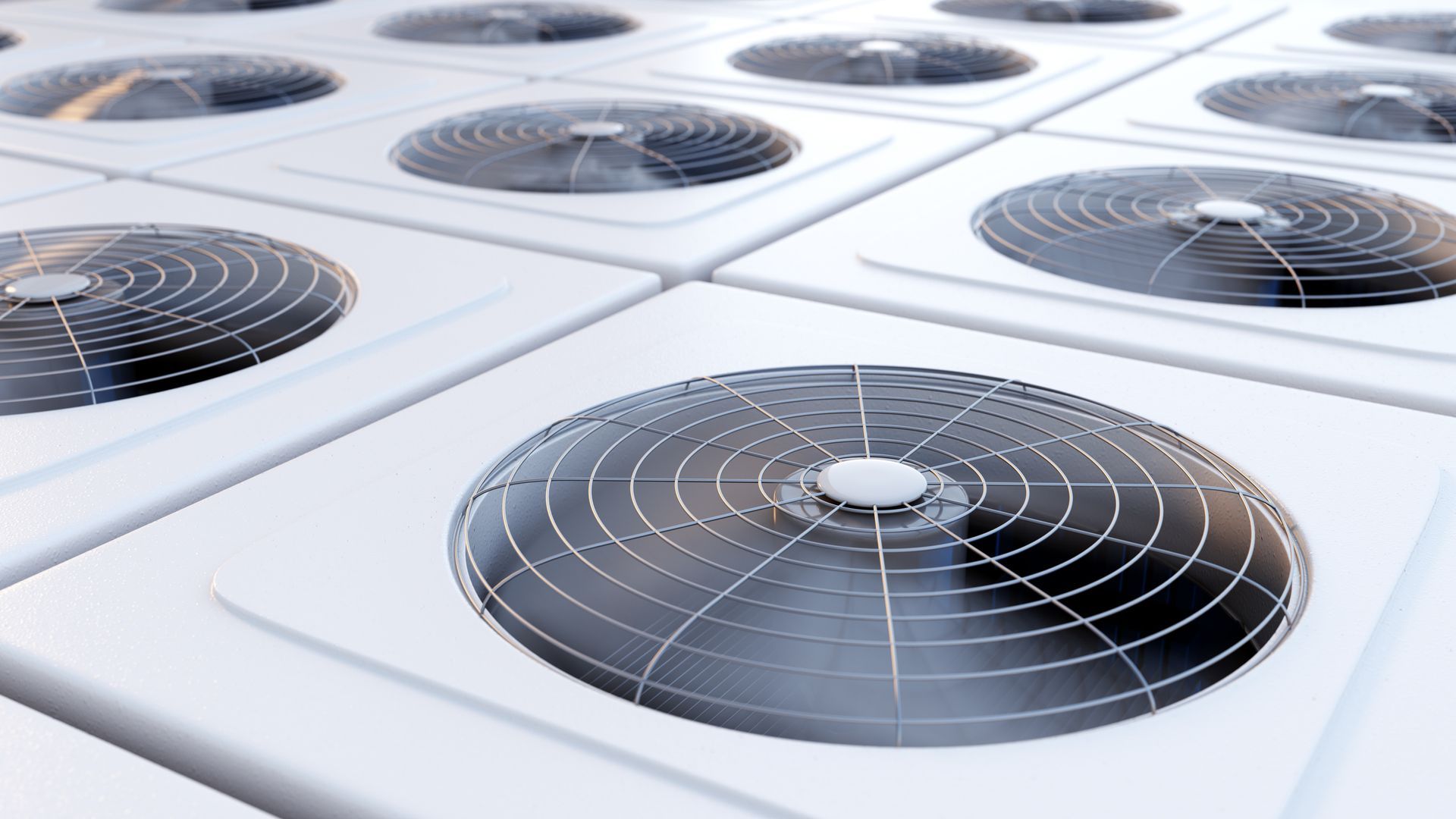
5 Signs Your Commercial HVAC System Needs Immediate Attention Your commercial HVAC system is the heart of your business's comfort and operational efficiency. When it's working properly, you barely notice it. But when something goes wrong, it can create a costly disruption—impacting everything from employee productivity to customer satisfaction. Recognizing early signs of HVAC problems can help you avoid expensive emergency HVAC repairs or complete system replacements. Here are five warning signs you should never ignore. 1. Unusual Noises Commercial HVAC systems typically run quietly in the background. If you start hearing banging, clanging, squealing, or grinding noises, it's a clear signal that something is wrong. Possible causes: Loose parts, worn bearings, motor issues. Why it matters: Ignoring unusual sounds can lead to major component failures and higher repair costs. If your HVAC system suddenly sounds like it's struggling, it’s time to schedule an immediate inspection with a trusted commercial HVAC maintenance provider like Evolution Maintenance. 2. Inconsistent Temperatures Are some rooms freezing cold while others feel stuffy and warm? Uneven heating or cooling is more than just an inconvenience—it’s a red flag. Possible causes: Blocked vents, failing compressors, thermostat malfunctions, or ductwork problems. Why it matters: Temperature inconsistencies strain your system and drive up energy bills. Properly diagnosing and fixing these issues early prevents unnecessary energy waste and discomfort for employees and customers alike. 3. Sudden Spike in Energy Bills If your utility bills have shot up without a clear explanation, your HVAC system may be working harder than it should. Possible causes: Dirty coils, clogged filters, refrigerant leaks, or malfunctioning parts. Why it matters: High energy consumption means your system isn’t running efficiently, costing your business money month after month. Scheduling regular commercial HVAC inspections can help pinpoint inefficiencies before they become long-term financial drains. 4. Frequent Cycling If your HVAC system is constantly turning on and off (known as "short cycling"), it's struggling to maintain the desired temperature. Possible causes: Thermostat issues, refrigerant leaks, oversized equipment, or electrical malfunctions. Why it matters: Short cycling stresses your system, causing faster wear and higher repair costs. This behavior can significantly shorten the lifespan of your HVAC unit if not addressed quickly through professional HVAC servicing.\ 5. Poor Indoor Air Quality Bad smells, excessive dust, or a sudden rise in allergy symptoms among employees could point to HVAC system problems. Possible causes: Mold growth, dirty filters, clogged ducts, or stagnant moisture. Why it matters: Poor indoor air quality not only affects health but can also open your business to liability issues and customer complaints. An experienced commercial HVAC technician can assess and resolve indoor air quality problems to keep your environment safe and inviting. Don’t Wait—Protect Your Investment Delaying action when your commercial HVAC system shows warning signs can lead to higher repair costs, lost business, and even complete system failure. Being proactive is key. At Evolution Maintenance, we specialize in rapid response and preventative care for commercial systems of all sizes. If you notice any of these warning signs, don’t hesitate—contact us today for an immediate assessment and expert repair services.
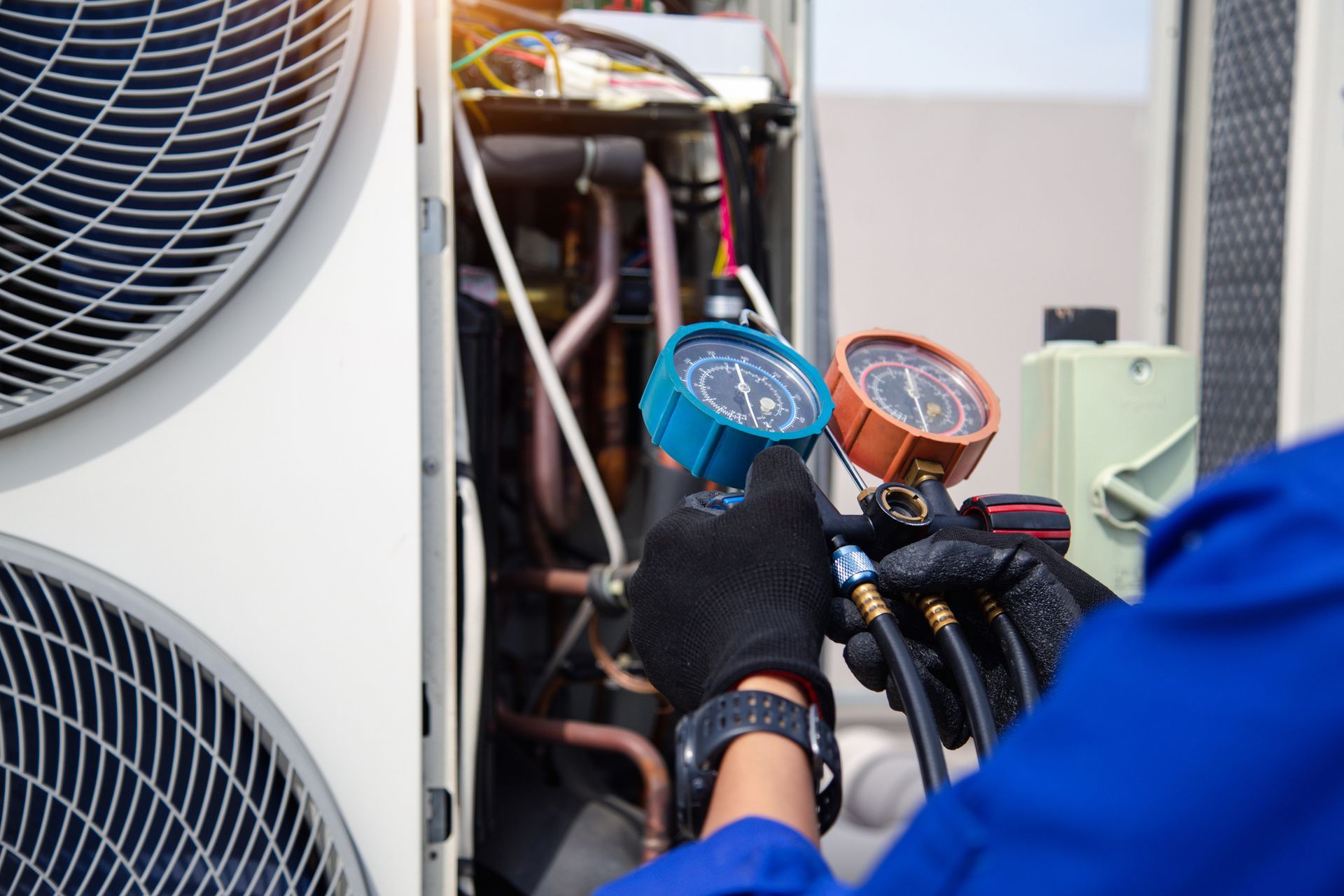
PROTECT YOUR BUSINESS WITH HVAC MAINTENANCE When you manage a business, every dollar matters. One often-overlooked strategy for safeguarding your company’s finances is simple: regular HVAC maintenance. Your heating, ventilation, and air conditioning systems aren't just a comfort feature—they are critical to your operations. Investing in preventative HVAC maintenance can lead to significant savings, improved performance, and a healthier, more productive work environment. The True Cost of Neglected HVAC Systems Ignoring routine commercial HVAC services might seem like a cost-saving measure in the short term, but it often leads to major expenses down the line. Dirty filters, worn-out components, and neglected inspections can cause your systems to work harder, driving up energy costs and increasing the likelihood of unexpected breakdowns. According to industry studies, businesses that skip routine HVAC maintenance face repair costs that are 30% higher on average—and a complete system failure could mean a five-figure replacement cost. Downtime, especially for retail stores, restaurants, or office buildings, also results in lost revenue and unhappy clients or employees. Benefits of Routine HVAC Maintenance Partnering with a trusted provider like Evolution Maintenance for regular HVAC check-ups offers a range of financial advantages: 1. Lower Energy Bills Efficient HVAC systems consume less power. Regular cleaning, lubrication, and inspections ensure that your equipment operates at peak performance, reducing your monthly utility expenses. 2. Extended Equipment Lifespan A well-maintained HVAC system can last up to 40% longer than one that’s neglected. This delays costly replacements and maximizes your original investment. 3. Fewer Emergency Repairs Preventative HVAC maintenance identifies potential issues before they turn into expensive emergencies. Scheduled inspections and tune-ups help your business avoid costly surprise repairs that can disrupt operations. 4. Improved Indoor Air Quality Cleaner air means healthier employees and customers. Regular filter replacements and system cleanings reduce allergens, mold, and bacteria, leading to fewer sick days and a more comfortable environment. 5. Compliance and Safety Regular inspections ensure your systems meet local codes and safety regulations. Non-compliance can lead to fines, insurance issues, or even shutdowns—all of which can hit your bottom line hard. How Often Should You Schedule Commercial HVAC Maintenance? The recommended frequency depends on your industry and usage levels, but most businesses should plan for professional HVAC servicing at least twice a year—typically in the spring and fall. Critical environments like healthcare facilities or food service operations may require more frequent checks. Evolution Maintenance offers customized HVAC maintenance plans tailored to your specific needs, ensuring optimal performance year-round. Protect Your Business's Future with Evolution Maintenance Regular commercial HVAC maintenance isn’t just an operational necessity—it’s a strategic financial decision. By keeping your systems running efficiently, you safeguard your bottom line, protect your people, and support the long-term success of your business. At Evolution Maintenance, we specialize in helping businesses just like yours thrive through proactive, reliable HVAC solutions. Contact us today to schedule your maintenance plan and see how easy protecting your investment can be.